Definition, Function, and Elements of a Suspension System
In any vehicle, a suspension is the set of levers and elastically deformable elements that binds the unsprung masses (wheels and, usually, brakes) to the suspended masses (chassis and body).
When a two-track vehicle turns, it rolls outwards because of inertia, causing the compression of the outer suspension and the extension of the inner one. Compression and extension happen also when the vehicle travels on rough surfaces. A vehicle suspension system allows these compression and extension movements while performing the following three functions:
- maintaining the body at the right height from the ground
- attenuating the oscillations of the vehicle due to its inertia and road bumps
- putting the tires in the best possible conditions to transmit the forces to the ground.
Any suspension is made up of three main components:
- a kinematics, that is, the set of levers that guides the wheels in their motion with respect to the body
- an elastic system that provides the force needed to suspend the vehicle, control its movements due to inertia, and attenuate the shocks coming from the road bumps
- a damping system which attenuates the oscillations of the elastic system to avoid bouncing.
The elastic and damping systems have the task to control the car body movements, with great influence on handling and comfort. Kinematics is what the elastic and damping systems need to do their job in the best way, that is, avoiding undesired variations of the wheels angles, such that would negatively affect the trajectory of the vehicle and the tires grip.
In the present article we will focus on kinematics.
Categories of suspension kinematics
There are three different categories of suspension kinematics:
- dependent or interconnected suspensions
- semi-independent suspensions
- independent suspensions.
In dependent or interconnected suspension, the two wheel hubs on the same axle are connected to each other through a rigid structure, therefore the motion of a wheel always affects the other.
In semi-independent suspension, the wheel hubs are connected to each other through a structure that allows some flexibility.
In independent suspensions, the wheel hubs are connected to separate suspensions, therefore they are free to move independently.
This kind of suspension is often paired with an anti-roll bar, i.e., a flexible bar that connect the suspensions to each other and helps reducing the body roll due to inertia in curves while mantaining a soft behavior on bumps. When this happens, an independent wheel suspension actually becomes to some extent a semi-independent system.
Main Kinematics Measures
Camber is the inclination of the wheels from the vertical when viewing from the front of the car.
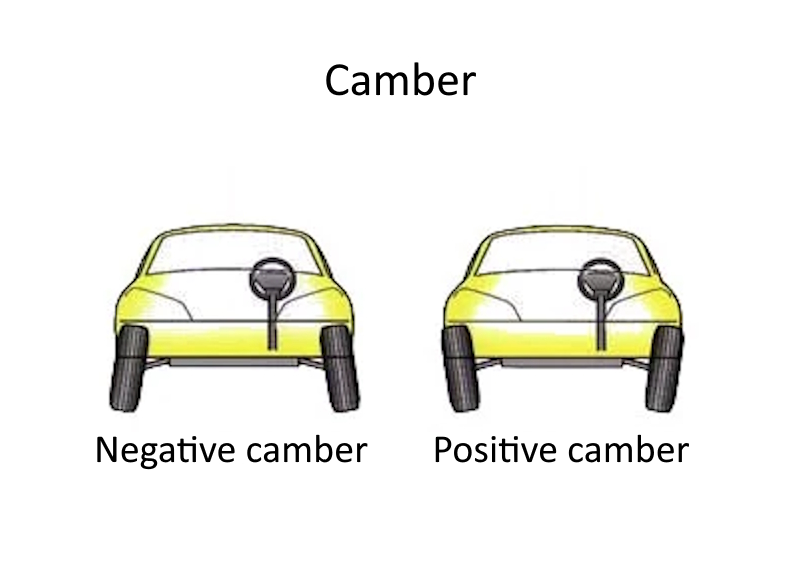
- Positive camber is when the top of the wheel is laying outwards
- Negative camber is when the top of the wheel is laying inwards
On road cars, camber is typically set between 0 and -1.0 degree.
In general, an easy way to increase cornering performance along with matching suspension and tire upgrades, is to dial in some extra negative camber. For most performance road cars, a suitable camber setting is in the range of –1.0 and –2.0 degrees. One advantage of this is that as the centrifugal force during hard cornering causes the body of the car to roll outwards, the outside tires which take the brunt of the cornering force, will sit more upright relative to the ground, maximizing the tread to road contact and ultimately resulting in more grip. However, dialing in too much negative camber can have adverse effect not only on the more obvious tire wear, but also on performance as well as safety, stability and driving pleasure.
Toe angle is the angular position of the wheel when viewing from the top expressed in degrees.
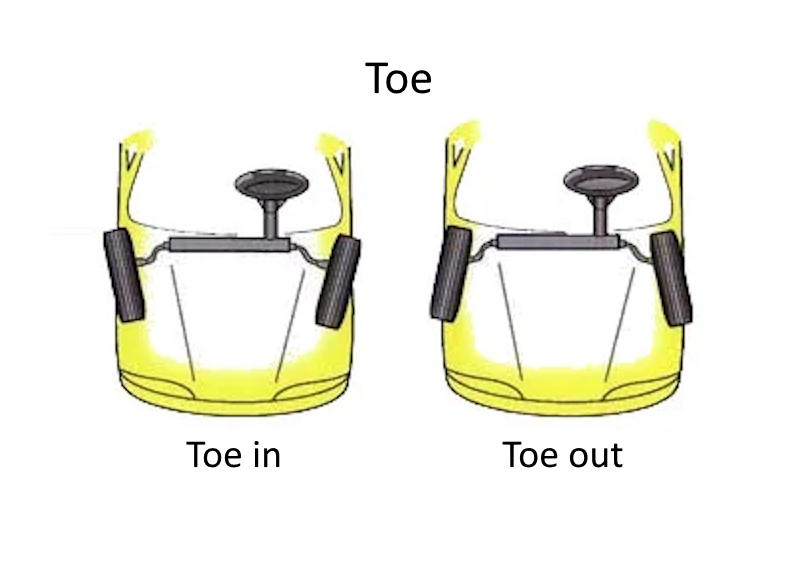
- Neutral Toe: both wheels are pointing straight ahead.
- Toe-in: the front of the wheels are closer together then the rear.
- Toe-out: the front or the wheels are further apart then the rear.
Typically, on most road cars the toe is set to between neutral and some toe-in. Generally, toe-in improves stability and reduces nervousness, while neutral to toe-out improves turn-in and sharpness.
Caster is the inclination of the steering axis from the vertical measured from the side of the car.
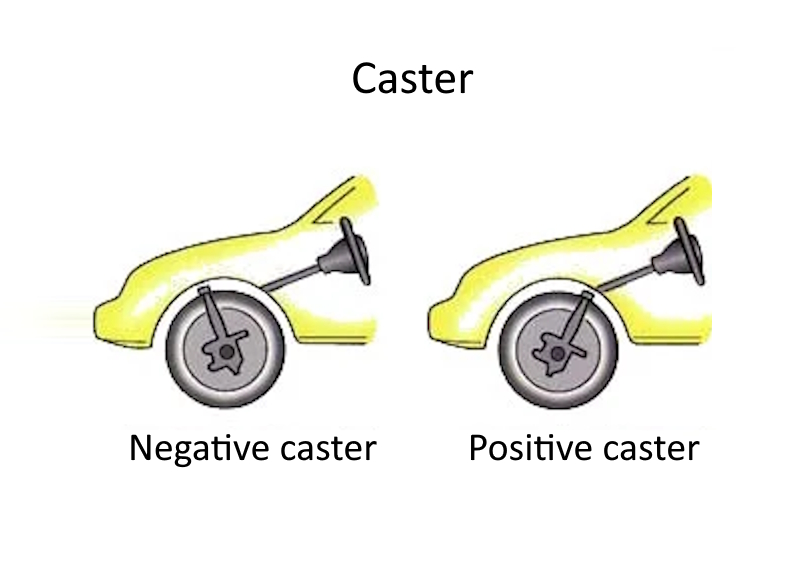
- Positive caster is when the upper pivot is behind the lower pivot.
- Negative caster is when the upper pivot is in front of the lower pivot.
While steering, the caster generates:
- a vertical displacement of the body
- an increase of the wheels camber.
Kingpin, like caster, refers to the inclination of the steering axis from the vertical, but seen from the front of the car.
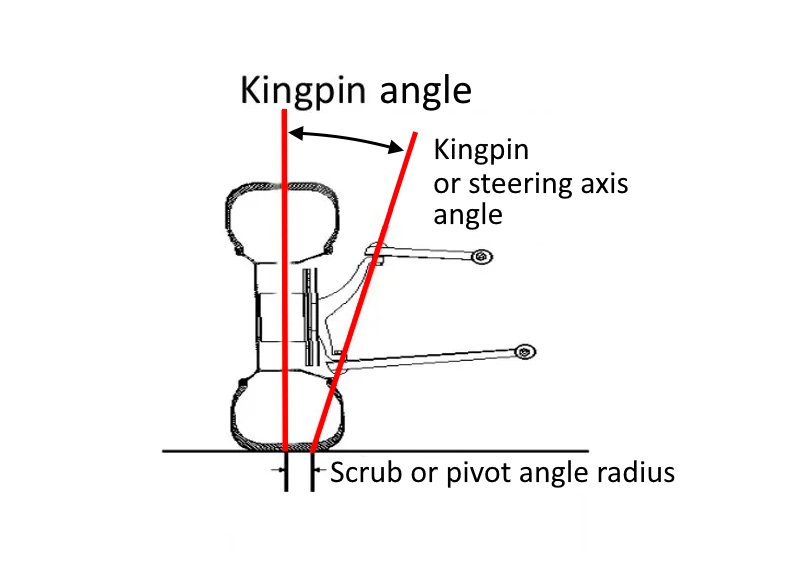
Similarly to caster, the kingpin angle is important on steering and affects:
- the wheel camber
- the body vertical displacement,
but the caster has the same effect on both wheels, while a kingpin angle makes the effect different on each wheel.
In general, a positive caster leads to the following benefits:
- Increased dynamic negative camber in turns
- Improved high speed stability
- Improved road feel, steering feedback and sensitivity
- Increased steering weight, useful to overcome some over-compensating power steering systems
- Improved steering turn-in response during corner entry.
Kinematics systems
Let’s now take a closer look at the existing suspension schemes, their respective pros and cons and how these schemes influence comfort, handling, dynamics, and driving pleasure.
Rigid Axle Suspension
It is the most common interconnected wheel suspension system. The wheel hubs are rigidly connected by a transversal beam, which in turn is linked to the chassis by two simple leaf springs. In more refined applications coil springs are used instead, paired by two trailing arms and a Panhard rod ─ i.e., a diagonal transverse bar linked to the chassis on a side and to the axle on the opposite side ─ to control longitudinal and lateral movements. On drive axles, the shaft becomes much heavier, because it contains the axle shafts and the differential.

Pros
- Sturdy, therefore ideal for transporting heavy loads
- Cost effective
- No camber variation on smooth roads even when the vehicle rolls
- No toe angle variations in any situation.
Cons
- It requires a lot of free room under the chassis
- When used on a drive axle it is heavy, therefore it has high inertia on bumps (less comfort and grip)
- The vertical motion of a single wheel on a side bump causes a variation of camber on both wheels (less grip, driving precision and comfort)
- Unlike the torsion beam suspension, it cannot be tuned to have a slight steering behavior
Still the benchmark on trucks and off-road vehicles, it was very common as a rear suspension on rear-wheel-drive cars, especially in America (but also in many Fiat sedans until the mid-1980s.
De Dion Suspension
Another example of interconnected wheel suspension system, the De Dion bridge is basically a light version of the rigid rear wheel drive axle where the differential and the axle shafts are fixed to the chassis insgtead of being in the axle, to reduce the unsprung masses inertia. For this reason, the transversal beam is U-shaped.
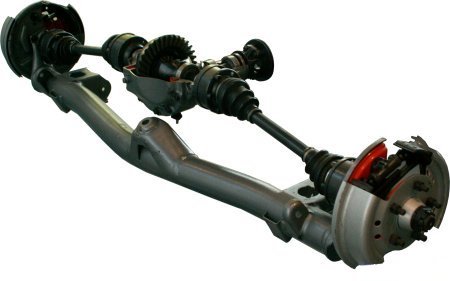
Pros
- No camber variation on smooth roads even when the vehicle rolls
- No toe angle variations in any situation
- Low inertia (much more grip and comfort on rough surfaces than the rigid axle).
Cons
- The vertical motion of a single wheel on a side bump causes a variation of camber on both wheels
A particularly sophisticated version of this kinematics was used in many Alfa Romeo rear-wheel drive models from the 70s to the 90s. In these cars, the gearbox and the brake rotors were attached to the differential, to improve weight distribution and reduce the unsprung masses. The recent rear-wheel drive Alfa Romeo models feature a multi-link system.
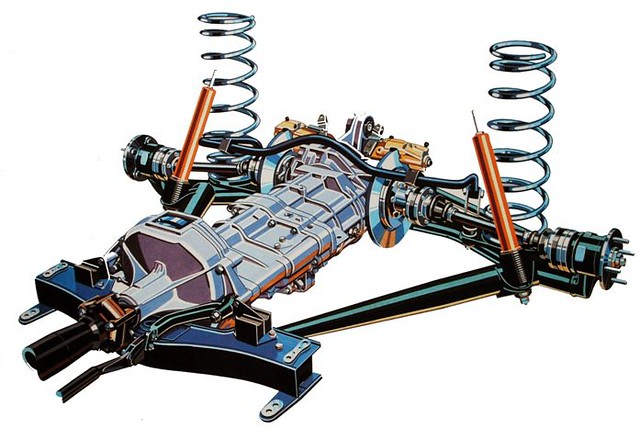
The De Dion Suspension still survives in the little Smart car, where the whole engine and transmission is contained in the U-shaped arm.
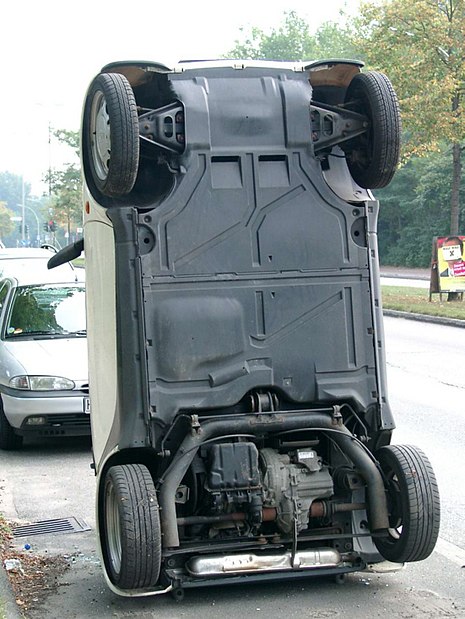
Torsion Beam Suspension
It is a semi-independent suspension system based on a single U-shaped elastic beam that on the front part is hinged to the chassis via rubber bushings while both wheel hubs are connected to the rear tips of the U. These are not orthogonal to the beam, thus allowing the possibility to control to a certain extent the camber and toe angle variation on roll and asymmetrical bumps.
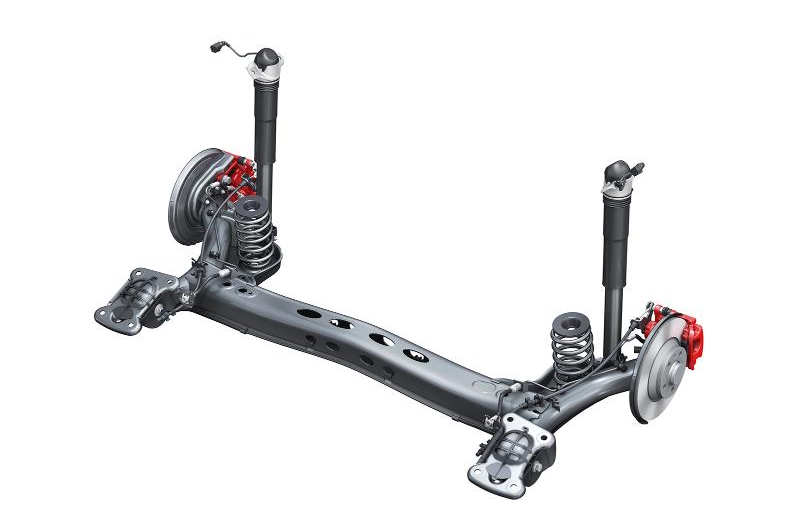
Pros
- Very simple construction
- Very cost effective
- Low inertia (much more grip and comfort on rough surfaces than the rigid axle)
- Good control of camber and toe angle
- It can be designed in a way to give the wheels a slightly steering behavior on roll, to improve handling and stability.
Cons
- It is not as good as a double wishbone or a multi-link suspension.
Simple and effective, the torsion beam system is nowadays the most common solution for the rear suspension on front-wheel-drive cars.
Swing Axle Suspension
This is a very simple and old independent wheel system where each wheel hub is fixed to the outer end of a transversal triangular arm, whose inner ends are hinged to the chassis or to the differential. It can also feature simple arm with supporting trailing arms to control longitudinal movements.
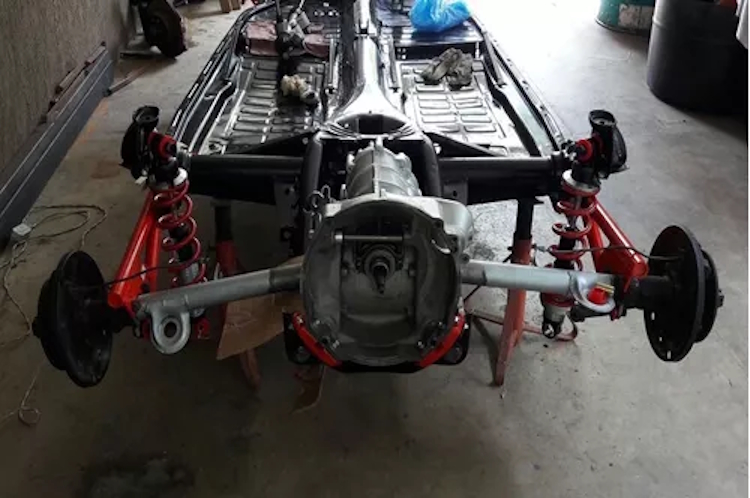
Pros
- Simple
- Low inertia
- Cost effective
- No toe angle variations in any situation.
Cons
- Any movement of the wheel leads to a camber variation, with bad handling both in curves ─ where it sports an evident oversteering behavior ─ and on bumpy roads. To minimize the oversteering, this kinematics was often tuned with a positive camber in normal condition, so to have a good neutral camber when the body leans in a curve because of inertia, but this made the handling inaccurate on straight lines.
The swing axle suspension was very common on family models like the VW Beetle until 1969, when it was replaced by a semi-trailing arm suspension, and all compact Fiat models from the mid-1950s to mid-1980s, eventually replaced by torsion beam systems.
This kinematic was also used in the 1940s and 1950s on sports cars like Porsche 356 and Mercedes-Benz 300SL “Gullwing”, models famous for their handling unpredictability. In both cases they were replaced by semi-trailing arm systems.
Trailing Arm Suspension
It is another very simple independent wheel system where each wheel hub is fixed to a longitudinal rod, whose other end is hinged to the chassis. Typically, in this scheme the wheel is pulled, i.e., it is located behind the rod. On some french compact cars it was used as a front suspension with the arms behind the wheels.
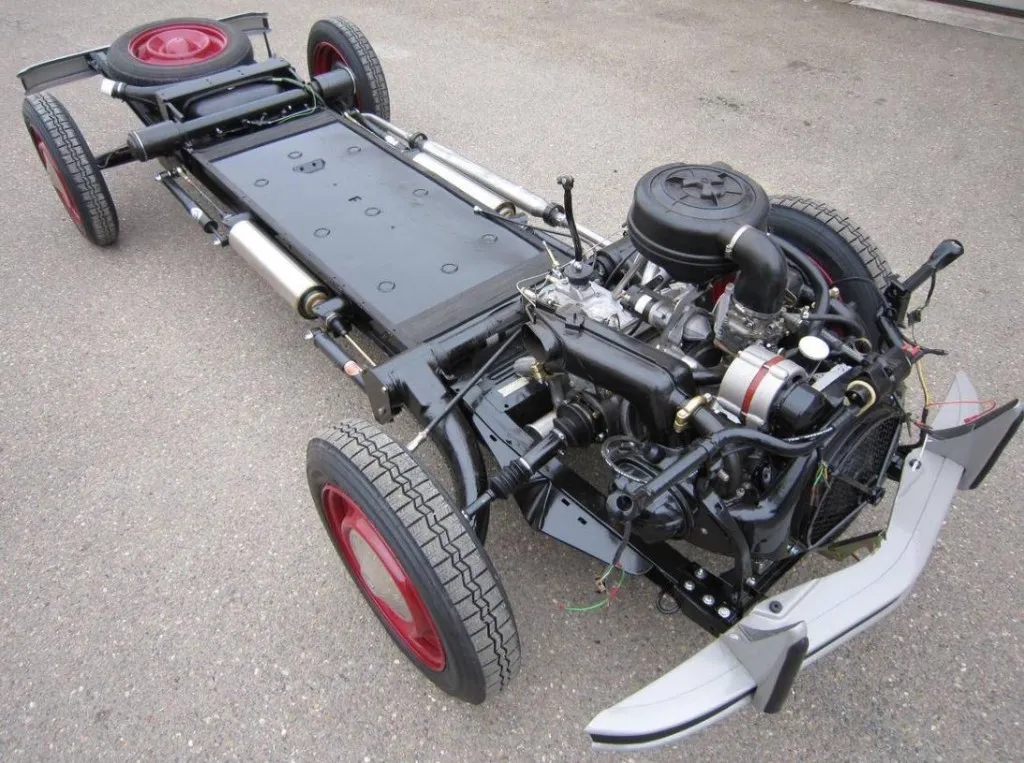
Pros
- Simple
- Low inertia
- Cost effective
- No toe angle variations in any situation
- Very good behavior on asymmetrical bumps
Cons
- When the body rolls, the wheels follow the body leaning outwards, therefore the camber changes dramatically, leading to an understeering behavior. That is why all cars equipped with this kinematics sported tight, almost motorcycle-style tires.
- Under strong braking, the reaction torque generated by the brakes compresses the rear suspension and extends the front suspension, generating a powerful anti-dive effect, but dramatically reducing the comfort on bumps
- When used as a front suspension, its compression increases the caster, affecting the steering feedback and sensitivity
This kinematics was used until the 1990s on all Citroen and Renault compact cars. It was eventually replaced by McPherson system for the front suspension and torsion beam system for the rear one.
Incidentally, this system is used on all Vespas as a front suspension.
Semi-Trailing Arm Suspension
This kinematics is a compromise between the transverse arm suspension and the trailing arm suspension. Each wheel hub is fixed to the outer vertex of a right-triangle shaped swingarm, whose hypotenuse is oriented forward and is hinged diagonally to the chassis.
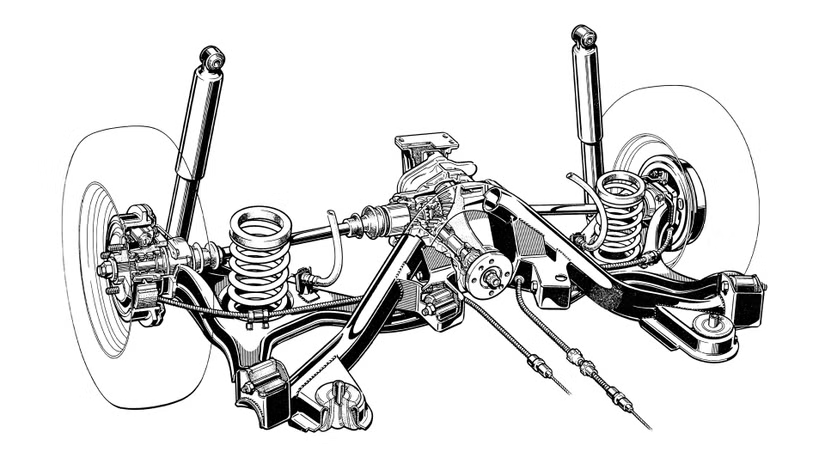
Pros
- Simple
- Lower inertia than a rigid axle
- Cost effective
- Much better behavior in curve compared to the trailing arm and the swing arm solutions, because the variation of camber on one wheel is compensated by an opposite variation on the other wheel.
Cons
- Asymmetrical variations of camber and toe on asymmetrical bumps, leading to inaccurate steering
- Camber and toe vary with the car load, leading to worse steering behavior and irregular tire wear in some conditions.
The semi-trailing arm system was the standard rear suspension on Mercedes-Benz, BMW, and Porsche models from the 1960s to the mid-1980s and it was eventually replaced by multi-link systems.
McPherson Suspension
The McPherson suspension system is an independent wheel system. Each wheel hub is linked to a vertical strut with a structural function made by a cylindrical coil spring mounted coaxially on a shock absorber. The top of this element is constrained by a bearing to an anchoring point of the body while the bottom is linked to a single triangular swingarm hinged to the chassis. Thanks to its construction simplicity, compactness and low design cost, this is the most used front suspension system, especially on front-wheel drive cars.
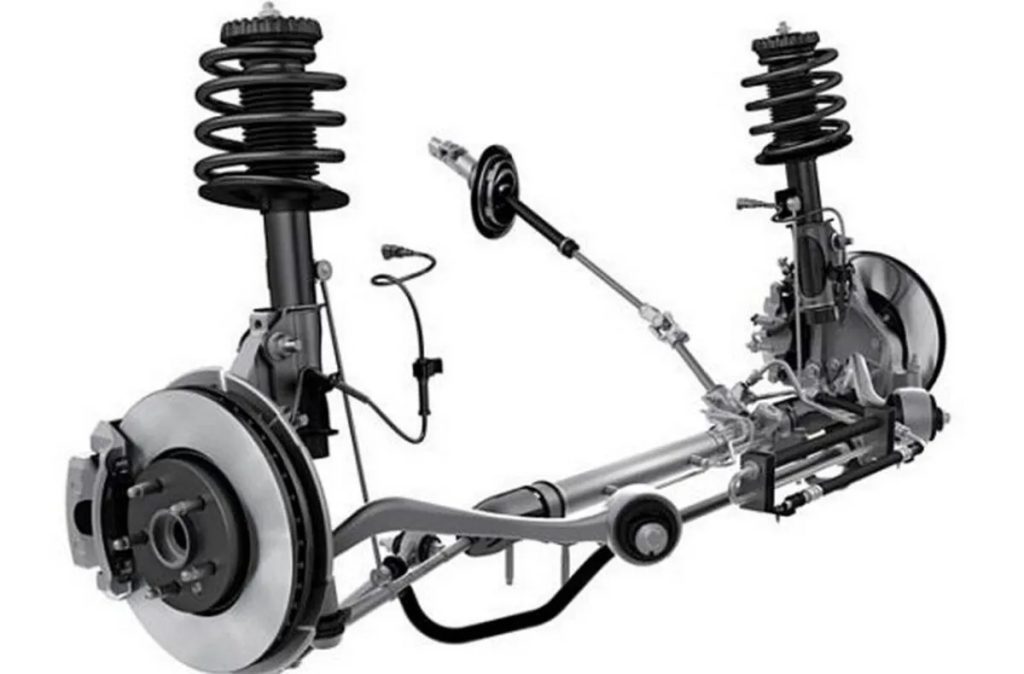
Pros
- The simplest solution for steering suspensions
- Low inertia
- Cost effective
- Leaves a lot of room for the engine bay or the trunk
- No toe angle variations in any situation.
Cons
- When the suspension is compressed, the wheel takes a positive camber due to the fixed top bearing and the lower swingarm, making the steering somewhat inaccurate
- The struts can transmit some road impacts to the steering system, further worsening the steering feel
- Limited adjustability compared to more complex suspension systems, which limits the fine-tuning of handling characteristics
- It cannot be installed on sports cars with a low hood
Double Wishbone suspension
Characterized by two oscillating and overlapping triangular wishbones, one lower and one upper, it is one of the most effective schemes. If well designed, it allows the wheel to be guided with absolute precision, varying the camber angle during the excursion in order to keep it as constant as possible with respect to the ground. By varying the length and arrangement of the arms, it is also possible to vary the roll center position, i.e., the point around which the chassis rotates when cornering, as desired. The upper arm is generally shorter than the lower one to ensure appropriate camber control while rolling.

Pros
- Very precise handling
- Low inertia = great comfort and grip
- Perfect control of toe angle
- Good control of camber
- No negative effects on steering accuracy
- It can be designed in a way to give the wheels a slightly steering behavior on roll, to improve handling and stability
- Easy to tune
Cons
- Expensive to design and build
- It leaves less room for engine bay or trunk compared to other suspension systems
The double wishbone kinematics is featured as front suspension on all our Mazda MX-5 series as well as on all our Mercedes-Benz SLK and E series, and as rear suspension on our NA and NB series.
Multi-link Suspension
In the multi-link suspension each wheel hub is linked to the body by multiple rods, from three to 5. A well designed 5 rods multilink system is the most perfect possible kinematics, because it assures the best control of wheel movements, which results in the best overall handling, steering accuracy, and comfort compromise.
The first car to be equipped with a multi-link kinematics was the 1969 Mercedes-Benz experimental model C111. The first marketed model was the 1983 Mercedes-Benz 190E.
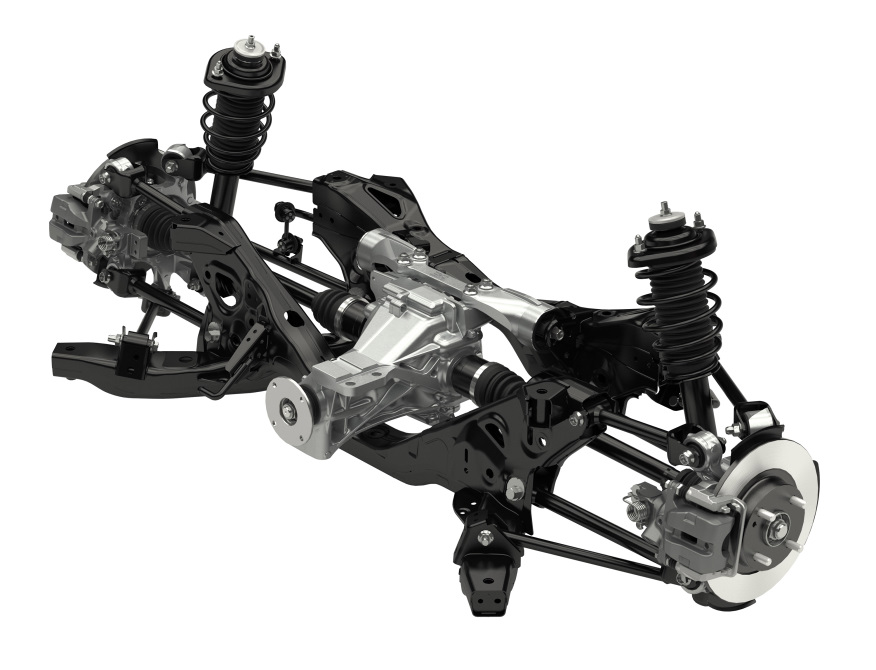
Pros
- Very precise handling
- No negative effects on steering accuracy
- Low inertia = great comfort and grip
- Perfect control of camber and toe angle
- It can be designed in a way to give the wheels a slightly steering behavior on roll, to improve handling and stability
- Low kinematics, it does not require a tall hood.
Cons
- Extremely expensive to design, it requires sophisticated CAD technique
- Very expensive to build
- Expensive to align and repair
- Impossible to tune, therefore it is not good for race cars
- It leaves less room for engine bay or trunk compared to other suspension systems
This scheme is featured as rear suspension on our Mazda MX-5 NC and ND series as well as on all our Mercedes-Benz SLK and E series.